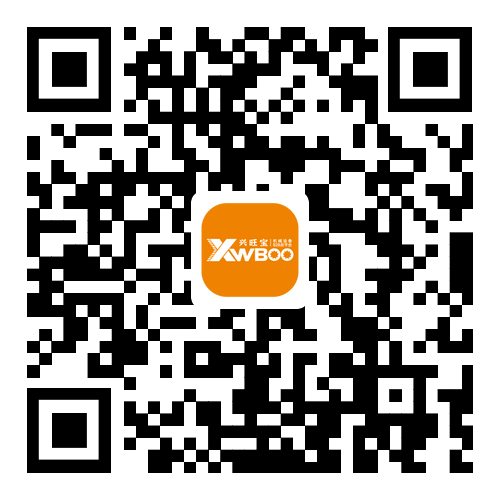
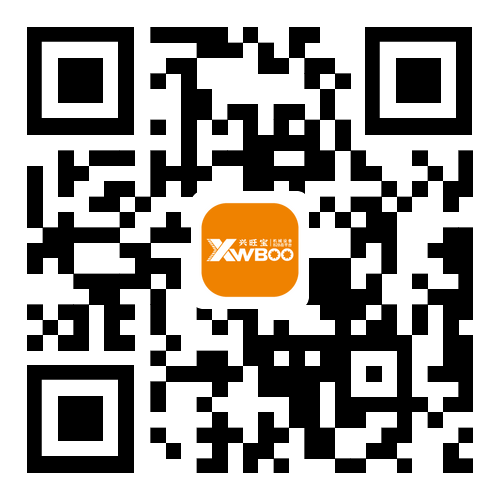
产品详情
4 检验类别
4.1 检验:
4.1.1 在下述情况下,必须检验后,才能开始加工:
4.1.1.1 工作班开始加工的个工件;
4.1.1.2 调换操作者后加工的个工件;
4.1.1.3 更换(调整)工艺装备或更换模具后加工的个工件;
4.1.1.4 更换材料批(炉)号后加工的个工件;
4.1.1.5 代用材料后加工的个工件。
4.1.2 检验的依据:a)工艺图纸或工艺卡片;b)作业指导书(工艺控制点)。
4.1.3 检验内容:
4.1.3.1 根据检验工艺规程的要求,核对产品的质量特性值是否真正符合要求;对检验
合格,批准生产加工,检验不合格,进行不合格品的处理,同时分析不合格原因,采取改进措施后生产,产品继续检验,直至合格为止。
4.1.4 检验要求:
4.1.4.1 对,根据加工工艺要求,核实产品或工件(毛坯)产品的质量特性是否符合要
求。对检查的工件(毛坯),操作者必须做好自检和标识,在操作者缺乏检测手段时,也应对工件外观质量自检,合格后送检验员检查。无论在任何情况下,检验未经检验合格,不得进行批量生产或继续加工作业。
4.1.4.2 做好检验记录,要求按工件种类分类填写检验记录,以便追溯。
4.1.4.3 检验状态分为:合格、不合格、待检、检后待定;产品标识要求填写“工件名称、规格、
数量、尺寸、首检合格”要素,并放在产品的最顶端。
4.2 巡回检验:
4.2.1 由检验人员在生产现场,进行日常工艺纪律巡回监督检查,重点监控工序质量和工艺纪律。
4.2.2 根据检验工艺规程和作业指导书的要求、检验、核对巡检产品的质量特性值是否真正符合
要求。
4.2.3 若巡检某质量特性值不合格,应按《不合格品控制程序》处理,同时。立即对本次巡检与
上次巡检(或首检)间隔中生产的产品的不合格质量特性值逐件99%检查,剔除不合格品。
对巡检中剔除的不合格品按《不合格品控制程序》进行处理。
对投入批量生产的工件某尺寸在机加工过程中有争议时,应立即报告生产技术部进行分析性检查、仲裁性检测,必要时核实模具或工艺卡片,严禁不合格模具或工艺卡继续生产和现场毛坯流入下道工序。
4.3 完工检验(终检)
4.3.1 全部加工活动结束后,对半成品或完工的产品、零件进行综合性的核对工作,核对加工件
的工序是否全部完成,有无漏序、跳序的现象存在,并分析原因,采取措施。
4.3.2 完工检验依据:a)工艺卡(图)或零件图;b)产品设计图样及作业指导书;c)合同规定或交